Annals of Burns and Fire Disasters - vol. X - n. 4 - December 1997
THE RISK OF TRANSPORTATION OF DANGEROUS GOODS: BLEVE
IN A TUNNEL
Ciambelli P.(1), Bucciero A.(1), Maremonti M.(1),
Salzano E.(2), Masellis M.(3)
(1)Dipartimento Ingegneria Chimica e Alimentare,
Università di Salerno, Via Ponte Don Melillo, 84084 Fisciano (SA), Italy
(2)CNR-GNDRCIE, P.le V.Tecchio 80, 80125 Naples
(3)Divisione di Chirurgia Plastica e Terapia delle Ustioni, Ospedale Civico, Palermo
SUMMARY. Boiling liquid expanding vapour
explosion (BLEVE) is regarded as a major risk in the storage and transportation of
hazardous materials. Nearly all the cases reported in the literature refer to open
environments while BLEVEs in confined or congested areas are very uncommon. This paper
presents the case history of a BLEVE of a tank truck transporting LPG that occurred
in a highway tunnel near Palermo (Italy). The truck was involved in a car crash that gave
rise to the release of propane gas through a crack that formed on the top of the vessel.
The ignition of the gas cloud that was created caused critical burns in 25 persons. The
subsequent tank truck BLEVE caused five deaths. The accident was described by modelling
separately the deflagration of the gas cloud and the BLEVE. The evolution in time and
space of the deflagration was modelled with a computational fluid dynamics technique,
using a commercial code, while a beat transfer model was specifically developed in order
to simulate the pressure increase inside the vessel until the tank collapsed and the BLEVE
occurred.
Introduction
The evaluation of the risks involved in the transport
of dangerous goods on road and rail is of primary importance because of the different
substances and scenarios involved. Typical situations of concern are related, for
instance, to accidental releases in urban areas, where the consequences of an accident can
be catastrophic.
Liquefied petroleum gas (LPG) is particularly exposed to the risk of serious accidents
such as BLEVE (Boiling Liquid Expanding Vapour Explosion), i.e. explosion of a tank due to
rapid evaporation of the liquid contained caused either by a depressurization wave
generated by a hole accidentally formed in the tank shell or by an intense heat radiation
load due to an external fire. As a consequence of the tank failure, the tank is flattened
to the ground, giving rise to a strong blast wave, a destructive fire-ball, and in some
cases the formation of numerous fragments that can be propelled significant distances. The
characteristic time duration of a BLEVE usually ranges from 10 to 30 min, in the case of
full fire-engulfment. I The time can become significantly shorter in tunnels.
Several examples of BLEVEs are reported in the literature but they always refer to open
environment scenarios, while descriptions of accidents occurring in congested areas are
unavailable. Obstructions and confinement are nevertheless recognized as significant
factors affecting fire and explosion strength: road and rail tunnels must therefore be
considered sites of major risk.
This paper describes the deflagration of a gas cloud that formed in a road tunnel near
Palermo (Italy), followed by the BLEVE of a tank truck transporting LPG. The whole
phenomenon is modelled by means of techniques of computational fluid dynamics (CFD) and of
a heat-transfer model that describes the pressure build-up of a tank due to external
fire.Special emphasis is given to the analysis of the time of occurrence of the BLEVE in a
confined environment, which is of great importance for emergency operation planning.
Description
of the scenario
On 18 March 1996, a tank truck was involved in a car
crash in a highway tunnel near Palermo, Italy. The tunnel is 148 m long, 9.5 m wide, and
6.5 m high. It was a rainy day with a strong wind (43 m/s) and the ambient temperature was
about 10 'C.
The collision gave rise to the escape of propane gas through a crack that formed on the
top of the vessel. The ignition of this gas cloud and the subsequent BLEVE of the tank
caused fatal injuries to five persons. A further twenty-five persons were critically
burned by heat radiation.
Eye-witness accounts allowed the following reconstruction of the accident (Fig. I):
a vehicle (N° 1) skids about 100 m from the tunnel
entrance, causing a pile-up of cars
the engine of car N° 3 catches fire as a result of
collision with car N° 2
a tank truck enters the tunnel and stops about 50 m
from the exit, avoiding collision with the cars ahead
a bus, arriving at high speed, skids and crashes into
the tank truck, causing a leakage in the upper part of the tank shell, just below the
manhole. The tanktruck driver "feels" the presence of gas in the tunnel. About
one minute later a soft rumble is heard, followed by a hot wind that seriously burns the
people in the tunnel (burns in up to 50% body surface area in those nearest the tank). The
witnesses did not report the presence of a blast wave load
all persons quickly leave the tunnel, except for five
who feel faint as a result of the crash
four minutes later the tank explodes (BLEVE). The
resulting blast wave seriously damages the cars in the tunnel and kills the five persons
remaining there. Dense black clouds billow from the tunnel. Many traces of explosion are
found on the tunnel walls
Modelling of
the phenomenon
The rumbling noise and the hot wind causing burns to
the persons in the tunnel were due to the deflagration of the propane cloud that formed as
a result of the spill from the tank crack. Ignition occurred when the gas reached car N'
3, which was burning.
The hot burned gas produced by the cloud explosion and the jet-fire formed after the tank
leakage provided an intense heat radiation load to the vessel, causing the internal
pressure to build up to conditions of structural failure which normally occur at about 20
bar.' Knowledge of the leakage area is of primary importance for prediction of the
quantity of gas discharged during the first minute.
The post-incident analysis confirmed the presence, in the tank shell, of a crack measuring
about 20 sq cm. This area was probably enlarged by the jet-fire and the final BLEVE. The
crack area was evaluated by means of a beattransfer model (see below) simulating the
characteristic failure times for a totally fire-engulfed tank scenario.
Heat-transfer
model
The tank truck had a total volume of 10 cub m (diameter = 2.05 m, length = 3.6 m), with a
6-trun shell thickness. At the moment of the accident the tank contained 2500 kg of LPG
(filling percentage = 50%). No relief valve was fitted.
The BLEVE models available in the literature` are generally very sophisticated. These
models provide temperature profiles in the different tank zones (liquid, vapour, walls)
for different external fire scenarios and different regimes of thermal exchange to the
liquid zone (nucleate and film boiling regime). This detailed description is beyond the
scope of the present paper, which aims at the prediction of global characteristic BLEVE
properties, such as internal pressure build-up and tank failure time.
- The main
assumptions of the model are as follows:
On
the basis of these assumptions, the equations of conservation of energy for the liquid and
the vapour phase can be written as follows:
where
t is the time, Mliq, Mvap, Cvliq and Cvap are
the masses and specific heats of liquid and vapour, Thq, Tvap, Twall,vap
and Text are the liquid, vapour, dry wall and external temperatures, DHev, and DHsur, are the
latent heat of evaporation and the over-heating heat of vapour, Avap and Aliq
are the surfaces of walls enclosing vapour and liquid, Aliq is the surface of
liquid-vapour interface, and hr,liq is the radiative heat transfer coefficient
from the dry wall to the liquid. Uliq and Uvap are the overall heat transfer
coefficients from the external fire to the liquid and vapour respectively, defined as:
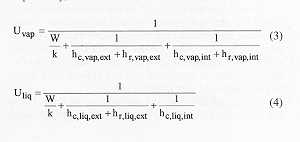
|
where
K is the thermal conductivity of the steel and hc,liq,ext , hc,vap,ext
, Hr,vap,ext , are the convective and radiative heat transfer coefficients from
external fire to the wet and dry surfaces, and hc,liq,int, hc,vap,int
and hr,vap,int, are the convective and radiative heat transfer coefficients of
the liquid phase and the gas phase. All coefficients were computed according to Aydemir et
al. and Rohsenow. Finally, a mass balance which takes into account the mass spilled from
the crack is included:
where
m0 is the initial amount of LPG, mtot, is the mass at time t, and Q
is the flow rate, modelled as sonic flow through an orifice:
where
C° is the discharge coefficient, g is the specific heat
ratio, Acrack is the area of the hole, M is the molecular weight of the
escaping gas, R is the ideal gas constant, and P is the internal pressure. Tank failure is
assumed to occur at 20 bar, which is generally reported as the maximum permitted pressure
for LPG tanks exposed to fire.
CFD
modelling of the vapour cloud explosion
The deflagration of propane gas released from the tank was simulated during the first
minute by means of a CFD code known as AutoReagas, developed by TNO (Netherlands) and
Century Dynamics Ltd (UK). The code solves the conservation equations of mass, energy and
momentum, using a finite volume method." The k-F, model" is included to describe
turbulence effects. The combustion is modelled as a single-step reaction from reactants to
products.
The accident scenario was reproduced using the CAD purchased with the code.
Results
Pressure
build-up inside the tank
Tle system of equations (1), (2) and was (5) solved using a Runge-Kutta method QV
order), yielding Tliq, Tvap and %, as functions of time. Internal
pressure was computed from Tliq.
Fig. 2 shows the model results, in terms of pressure increase in time, for
crack areas ranging from 5 to 50 sq cm. For each computation run, a delay time of one min
was assumed before full fire-engulfment condition were established. The case of a
completely closed vessel has also reported, for thye sake of comparison.
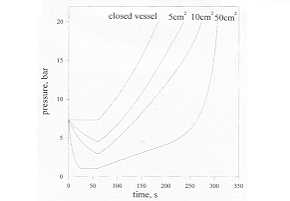
|
Fig.2 - Tank internal pressure
versus time for different crack sizes |
|
As expected,
the greater the crack area, the longer the time necessary to reach failure conditions (20
bar). The model produced a good prediction of failure time, as reported by witnesses,
assuming a crack area of 10 sq cm. The results of the model also show that, in the absence
of leakage, critical conditions are reached almost immediately.
The mass flow rate through the leakage is reported in Fig. 3, as a function of
time, for the area considered. A total mass of about 50 kg can be calculated as having
flowed through the crack in the first minute, i.e. prior to ignition. This amount of
propane was therefore used in the CFD simulation of the gas cloud explosion.
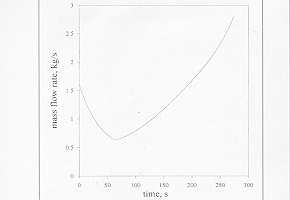 |
Fig. 3 - Mass flow rate history
trhought 10sq cm orifice |
|
CFD
simulation of the propone cloud explosion
The three-dimensional CFD modelling of the deflagration was carried out by assuming a
propane cloud at stoichiometric concentration (4%). The gas cloud was presurned to extend
from the tank truck to car N° 1, where ignition occurred.
Haine propagation along the tunnel, reported in Fig. 4 at different times, reached
its largest extent in about 1.7 seconds. Peak overpressures resulting from the model
simulation at various locations in the tunnel were of the order of 2kPa, which is
consistent with the "hot wind" felt by the persons present.
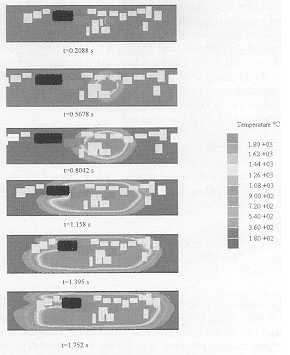 |
Fig. 4 - Modelled flame propagation
in road tunnel |
|
Conclusion
The description of the accident shows that the
characteristic times of BLEVE in confined areas such as road and rail tunnels are
significantly shorter than those in open environments. The rigid confinement provided by
the tunnel walls prevents the hot burned gas from exiting from the crash area, causing
rapid and complete fire-engulfment of the tank shell, thus accelerating the heating
process.
It is worth pointing out that the ignition of the vapour cloud that initially formed and
the subsequent fire should be regarded not only as precursors of the BLEVE but also as a
providential warning for the people who succeeded in escaping.
Thus, in order to define emergency planning with regard to the possible consequences of
the transportation of hazardous materials, the analysis must take into account the
geometrical characteristics of the areas involved.
RESUME. La BLEVE (boiling liquid
expanding vapour explosion: explosion de vapeur en expansion de liquide bouillant)
constitue un important risque dans l'emmagasinage et le transport des matériaux
dangereux. Presque tous les cas décrits dans la littérature traitent des environnements
ouverts, tandis que les BLEVEs en environnement clos ou encombré sont peu communs. Les
Auteurs décrivent la BLEVE d'un camion-citerne qui transportait du GPL (gaz de pétrole
liquéfié), explosion qui s'est produite dans un tunnel de l'autoroute près de Palerme
(Italie). Le camion avait été endommagé dans un accident de voiture qui a provoqué
l'échappement de gaz de propane à travers une fissure qui s'est produite sur le dessus
du citeme. Uignition du nuage de gaz qui a été créé a causé des brûlures critiques
à 25 personnes. La BLEVE successive du citerne a causé la mort de cinq personnes.
L'accident a été décrit en modelant séparément la déflagration du nuage de gaz et la
BLEVE. L'évolution dans le temps et l'espace de la déflagration a été modelée avec
une technique de la dynamique computationnelle des liquides, avec un code commercial,
tandis qu'un modèle de transfert de chaleur a été développé expressément pour
simuler l'augmentation de la pression à l'intérieur du citerne jusqu'à la BLEVE.
BIBLIOGRAPHY
- Birk A.M.: Scale
effects with fire exposure of pressure-liquefied gas tanks. J. Loss Prev. Process Ind., 8:
275-90, 1995.
- Davenport J.A.:
Hazards and protection of pressure storage and transport of LP gas. J. Haz. Mat., 20:
3-19, 1988.
- Pugh R.W.:
Quantify BLEVE hazards. Chem. Eng. Prog., 87: 66-72, 1991.
- Lees RP:
"Loss prevention in the process industries". Butterworth, Oxford, 1996.
- Beynon G.V.,
Cowley L.T., Small L.M., Williams L: Fire engulfment of LPG tanks: Heat-up, a predictive
model. J. Haz. Mat., 20: 227-38, 1988.
- Aydemir N.U.,
Magapu V.K., Sousa A.C.M., Venart J.E.S.: Thermal response analysis of LPG tanks exposed
to fire. J. Haz. Mat., 20: 239-62, 1988.
- Hadjisophocleus
G.V, Sousa A.C.M., Venart LE.S.: A study on the effect of the tank diameter on the thermal
stratification in LPG tanks subjected to fire engulfment. J. Haz. Mat., 25: 19-31, 1990.
- Ramskill PX.: A
description of the computer codes-codes to model the thermal response of an LPG tank
either fully or partially engulfed by fire. J. Haz. Mat., 20: 177-96, 1988.
- Rohsenow W.M.:
"Heat, mass, and momentum transfer". Prentice Hall, New Jersey, 196 1.
- Patankar S.V.:
"Numerical heat transfer and fluid flow". Taylor and Francis, Minnesota, 1980.
- Launder B.E.,
Spalding D.B.: "Mathematical models of turbulence".Academic Press, London, 1972.
This paper was received on 6 November 1997. Address
correspondenee to: Dr P. Cíambelli
Dipartimento Ingegneria Chimica e Alimentare
Università di Salerno
Via Ponte Don Melillo
84084 Fisciano (SA), Italy. |
G. WHITAKER INTERNATIONAL BURNS PRIZE
PALERMO, ITALY
Under the patronage of the Authorities of the Sicilian Region for 1998
By
law n. 57 of June 14th 1983 the Sicilian Regional Assembly authorized the President of the
Region to grant the Giuseppe Whitaker Foundation, a non-profit-making organization under
the patronage of the Accademia dei Lincei with seat in Palermo, an annual contribution for
the establishment of the G. Whitaker lnternational Burns Prize aimed at recognizing the
activity of the most qualified experts from all countries in the field of burns pathology
and treatment.
The amount of the prize is fixed at twenty million Italian Lire. The prize will be awarded
every year by the month of June in Palermo at the seat of the G. Whitaker Foundation.
The Adjudicating Committee is composed of the President of the Foundation, the President
of the Sicilian Region, the Representative of the Accademia dei Lincei within the G.
Whitaker Foundation, the Dean of the Faculty of Medicine and Surgery of Palermo
University, the President of the Italian Society of Plastic Surgery, three experts in the
field of prevention, pathology, therapy and functional recovery of burns, the winner of
the prize awarded in the previous year, and a legal expert nominated in agreement with the
President of the Region as a guarantee of the respect for the scientific purpose which the
legislators intended to achieve when establishing the prize.
Anyone who considers himself/herself to be qualified to compete for the award may send by
January 3 1 st 1998 a detailed curriculum vitae to: Michele Masellis M.D.,
Secretary-Member of the Scientific Committee G. Whitaker Foundation, Via Dante 167, 90141
Palermo, Italy. |
|